kWeld;s Story as told by Frank at keenlab
The story, as told by Frank. Frank is the creator of keenlab's kWeld.
If you want to make your own battery packs from LiIon round cells, then you have to solve the problem of connecting the individual cells. Soldering leads to them is not an option, because the required prolonged heat at the battery tabs tends to damage the cell's inner structure.I faced exactly this problem, and learned that the most common method to interconnect the cells is to weld nickel or nickel-plated steel strips across them using resistance spot welders.
The working principle of these is to push electrical current through metal strip and battery tab. As the metals have an electrical resistance, this current causes the material to melt together. The molten metal should only occupy a small area to prevent damage to the battery. This is accomplished by using a high current, allowing for very short pulses.
As this is a challenging task to achieve, professional welders start at several 1000$. There are cheaper models from a Chinese company, but I decided against this option... As I am an electronics engineer with quite some experience in power electronics, I decided to develop my own welder. It should be affordable for DIYers, more powerful and robust than comparable designs, and simple to use.
And I didn't like the fact that seemingly all spot welders would use a preset pulse length to set the weld intensity. The flowing current typically cannot be regulated, instead it varies with the electrical resistance of the weld spot itself. And that depends on quite a few factors like contamination, corrosion, and the mechanical force at which the metals are pushed together. The result is a variation in the amount of energy (=heat) that goes into the weld, leading to inconsistent results. To mitigate this effect, modern welders use two or more pulses, in order to soften the metals and burn away any contamination.
But there is a much more straight forward way to obtain consistent welds: If the amount of energy that is dumped into the weld spot is kept constant, then the same amount of metal is molten each time. This is what kWeld does. There is no need to experiment with time intervals, or the number of cleaning pulses. You just dial in the desired energy amount, and start working. The unit automatically adjusts the pulse duration to achieve the same result with each and every weld.
This picture shows the result of welding 0.15mm nickel strips to 18650 cells (source: eevblog forum, user "romantao"):
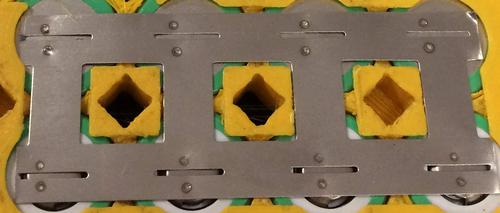
With the right power source, the kWeld unit is capable to weld pure nickel strips of up to 0.3mm thickness. But it is also agile enough to weld thin copper wires at low energies. The following picture shows a thin copper strand welded to a 2mm steel rod:
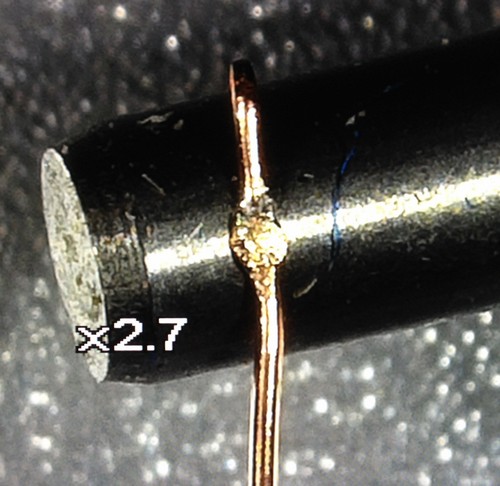
The assembly and operating manuals are available for download here:
https://www.keenlab.de/wp-content/uploads/2018/07/kWeld-assembly-manual-r5.0.pdfhttps://www.keenlab.de/wp-content/uploads/2018/07/kWeld-operation-manual-r3.0.pdf
The system firmware is upgradeable, allowing you to benefit from new features or improvements.
The latest firmware is available for download here:
https://www.keenlab.de/wp-content/uploads/2019/01/190128_kweld_release_r2_9.zip
This tool "link" is required to connect kWeld to a computer.
The necessary power supply for the welder is not part of the kit. It should ideally have an output voltage of 5 to 15V DC, and it should be able to deliver at least 1500A of current when short circuited for a few tens of milliseconds. As this is quite challenging to achieve, the following list gives some recommendations:
- Turnigy nano-tech 3S/5000mAh/130C Lithium Polymer battery (link). I have stress tested one of them for several complete discharge cycles, and it shows no visible swell thereafter. The measured current is 1300-1500 amperes.
- Turnigy graphene 3S/6000mAh/65C Lithium Polymer battery (link). These do not show any swell after a few full power discharge cycles, but I have no data on their life span yet. The current level is comparable with the nano-tech model.
- Ultracell UXL65-12 (link). According to feedback from a user, the current reported by kWeld is approx 1000A when tested with 0.15mm nickel strips.
- Bosch SMT 31-100 (link). According to feedback from a user, the welding current reported by kWeld is approx 1400A.
WARNING: Lithium Polymer batteries are potentially dangerous. If they fail internally, they can spontaneously self-ignite. It is therefore strongly advised to permanently supervise them during use and also while charging them, and to store them in a fire safe container when not using them.
You are dealing with very high energy levels when using this system, which may result in personal injury or fire when handled improperly. Take appropriate safety measures and use this system with caution. Never leave it unattended while being powered.
This product contains small parts, keep out of reach of children!
This system produces significant magnet fields, do not use it when you have a cardiac pacemaker!
The specs?
Hardware features (new features are highlighted in bold):- Input voltage for welding: 4V - 30V DC, enabling the use of ultracapacitors
- Extremely rugged MOSFET-based power switch and mechanical current bus design
- Fused overvoltage protection of internal power supply
- Maximum switch current: 2000A
- Power switch internal resistance: 120µOhm
- Pulse duration hardware watchdog: 250ms
- Under voltage lockout for power switch transistors
- Input voltage, output voltage, switch current, and logic supply voltage measurement
- Logic supplied directly from main power source - no need for a separate auxiliary power supply
- Screw terminal for external trigger switch
- Logic supply holdup capacitor during pulse firing
- user interface via an LCD, a dial/encoder, and a beeper
Software features (new features are highlighted in bold):
- Central weld control algorithm uses a Joule metering approach instead of a simple timer, eliminating the need for two-pulse firing and providing more consistent welds - the amount of energy that is deposited into the weld spot is always kept constant
- Ability to detect a failed weld, and acoustic feedback to the user
- Calibration procedure to cancel out electrode lead losses
- Manual mode, triggered from external switch
- Automatic mode, accompanied with a warning sound and triggered with an adjustable delay, once the system detects that both electrodes are in steady contact with the weld material
- Audible feedback of weld process completion
- Numeric feedback from an executed weld, assisting the user to achieve best results: pulse count, deposited energy amount, required pulse time for this energy, measured current flow, measured ohmic resistance of weld spot
- Simple and intuitive user interface - just adjust the desired weld energy up to 500 Joules with the dial knob; experience fine control from the use of an encoder
- Configuration menus accessible via dial's push button
- Overcurrent monitoring aborts pulse when triggered, protecting the power switch
- Battery monitoring with adjustable warning voltage
- Fuse fitness monitoring
- Firmware update interface